
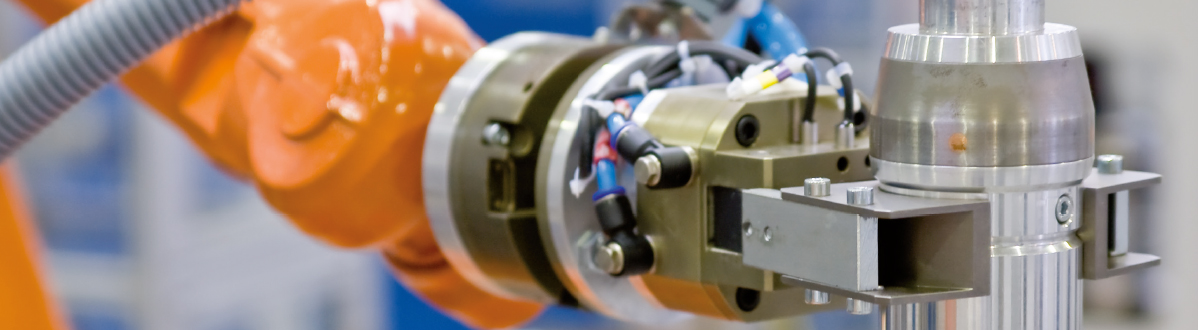



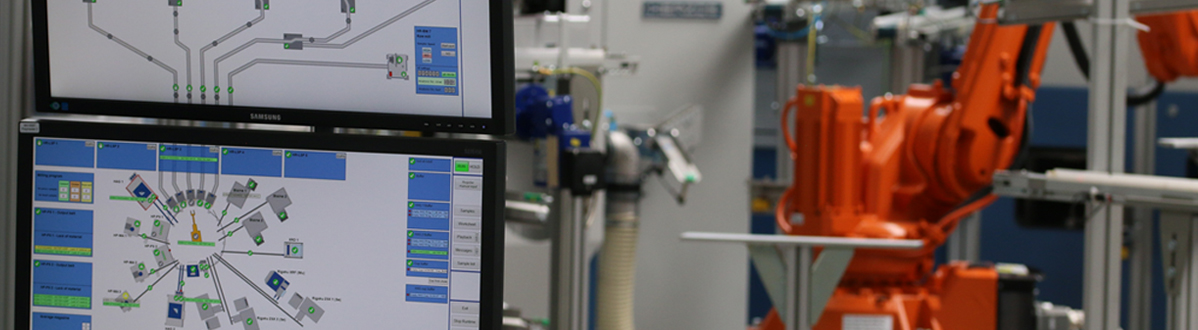
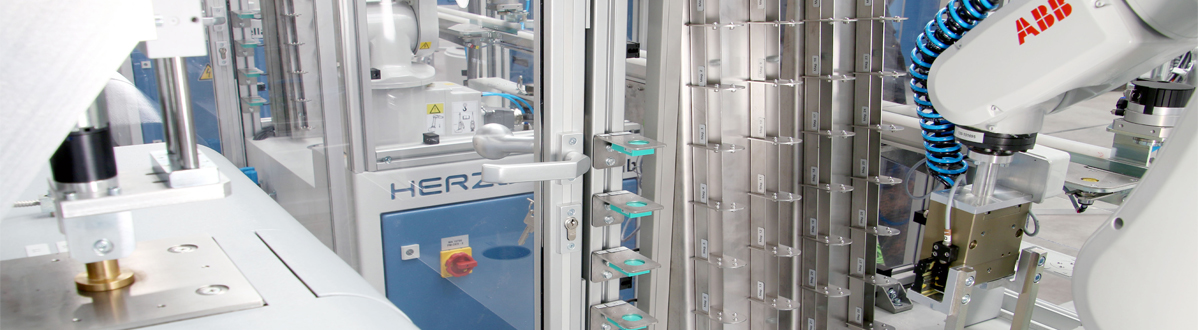
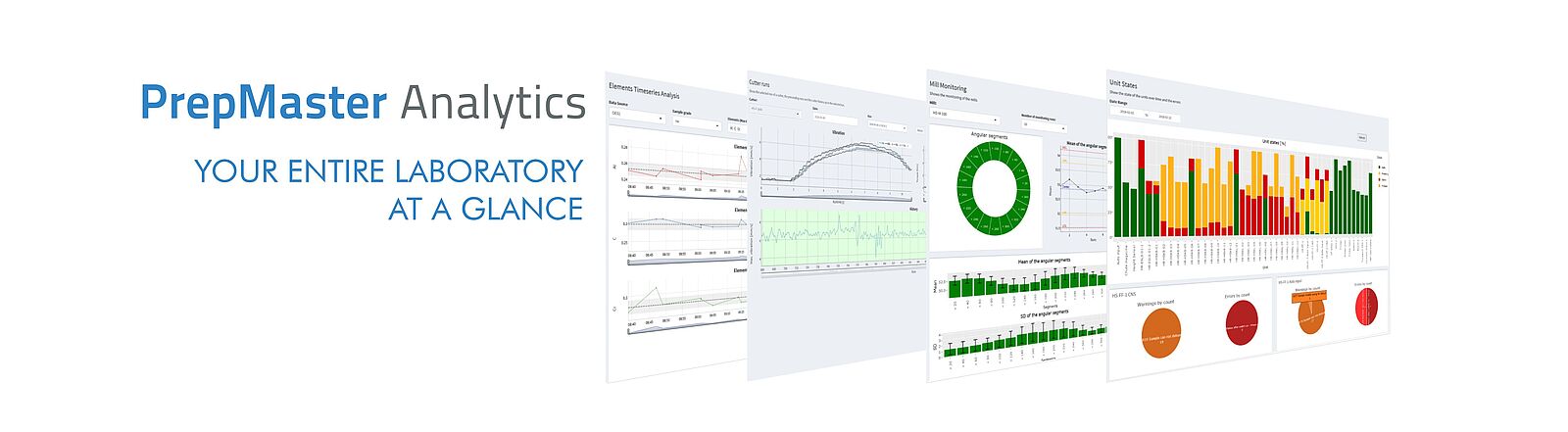

The large-scale solution for the fully automatic fusion process- Leading technology for highest level of laboratory quality and efficiency
Use
Preparation of fused beads (39 mm diameter)
Material
Different oxidic sample material,e.g., cement, slag, ores, ferroalloys (feed size 200µm)
Operation mode
Automatic
Fully automatic large-scale fusion system
The HAGSystem prepares oxidic sample materials for spectroscopic analysis. It uses a high-frequency fusion process which produces samples of exceptional analysis precision. The integrated scales are precise to 0.1 mg. The HAG is a fully automatic system for fusion. The system has following components: Input tray magazine, dosing module, fusion module, cleaning module. Plastic vials with 20 to 50g of sample materials are manually or automatically placed into the tray of the input magazine. All following steps are fully automated: Sample dosing for fusion, flux weighing, fusion and transport of fusion beads to the XRF, cleaning of crucibles and casting dish. The remaining sample and vial is returned to its original position in the tray.
High-precision dosing
The dosing unit consists of up to three dosing stations, a sample mixing station, buffer position for Platinum crucible, and a release agent dosing station. All stations are operated by a small robot. Samples in vials are placed into one of the three dosing units. For the fusion process, flux and sample are alternately weighed into the crucible to achieve an optimal dilution of both substances. Subsequently, the crucible is transferred to the mixing station, where flux and sample are mixed together. Optionally, a release agent can be added.
Efficient fusion
According to the sample load, the fusion module consists of 4, 6 or 8 heating stations. Each heating station has two heating positions for the crucible and the casting dish. A linear system transports the sample from the turntable to the heating station, fused bead to the XRF belt, and dirty crucibles and casting dishes to the cleaning station. The crucible is heated by induction. During this process, the sample can be swirled to aid the mixing. In parallel, the casting dish is heated to a predefined temperature. When the heating cycle is complete, the sample is automatically poured into the casting dish. The bead is allowed to cool within the casting dish. Depending on the sample type different cooling regimes can be used such as fast cooling with compressed air. The heating station is under control of a pyrometer. Before transported to the XRF, a special detector confirms that the fused bead is not cracked or moon shaped. Optionally, a camera system can be used to exclude that the bead is crystalline.
Automatic cleaning
The automated cleaning module for dirty crucibles and casting dishes consists of one or two ultrasonic baths, a washing station, and a drying station. 14 crucibles and casting dishes can be cleaned simultaneously in the ultrasonic cleaning station. All cleaning parameters can be adjusted with the PrepMaster system.